Cortes
Se
realizan mediante el torno, taladradoras, y fresadoras en otros procesos
ejecutados por máquinas herramientas con el uso de varias herramientas
cortantes. Las partes se producen desprendido materiales en forma de pequeñas
virutas. El trabajo central de estas máquinas está en la herramienta cortante
que desprende esas virutas. El corte de los metales tiene como objetivo,
eliminar en forma de viruta porciones de metal de la pieza a trabajar, con el
fin de obtener una pieza con medidas, forma y acabado deseado. Herramientas: Es
el elemento cortante que se utiliza en las máquinas herramientas con el fin de
realizar operaciones de mecanizado y dar un acabado a determinados materiales.
Separación de Virutas
Con este procedimiento obtenemos un producto final
arrancando virutas de los materiales en bruto.
1. Aserrado: Es la operación de corte con arranque de
viruta más común. En este grupo aparecen herramientas como las sierras y
serruchos. La operación de aserrado debe considerar el marcado del materia,
utilizando herramientas de trazado tales como escuadra, regla, compás y punta
de trazar (o lápiz). Se marcará por donde se deben realizar los cortes.
Estas herramientas poseen
una hoja de acero provista de dientes afilados y cortantes, capaces de cortar
materiales muy diversos como madera, plásticos, metales,… El diseño de los
dientes de las hojas se hace teniendo en cuenta el material que hay que serrar;
para cortar un material blando, como la madera, los dientes son más grandes y
están más separados que los que se utilizan para cortar materiales más duros,
como el hierro, que necesitan dientes más pequeños y más juntos.
2. Limado: El limado es una operación mecánica
mediante la cual se da forma a una pieza mediante el desprendimiento del
material en forma de limaduras. Las herramientas utilizadas para este fin son
las limas y las escofinas, que consisten en una barra de acero templado, de
superficie estriada, cuya misión es rebajar la pieza.
Se clasifican
según diferentes criterios:
- Tamaño (en pulgadas): A mayor longitud, mayor superficie a limar
- Forma: determinada por su sección transversal. Pueden ser planas, cuadradas, triangulares, de media caña, redondas.
- Tipo de picado: Es la rugosidad de la superficie del cuerpo metálico. Según el picado tenemos escofinas (de grano basto, sólo empleadas para maderas) y limas propiamente dichas (de grano fino, empleadas para metales o maderas muy duras).
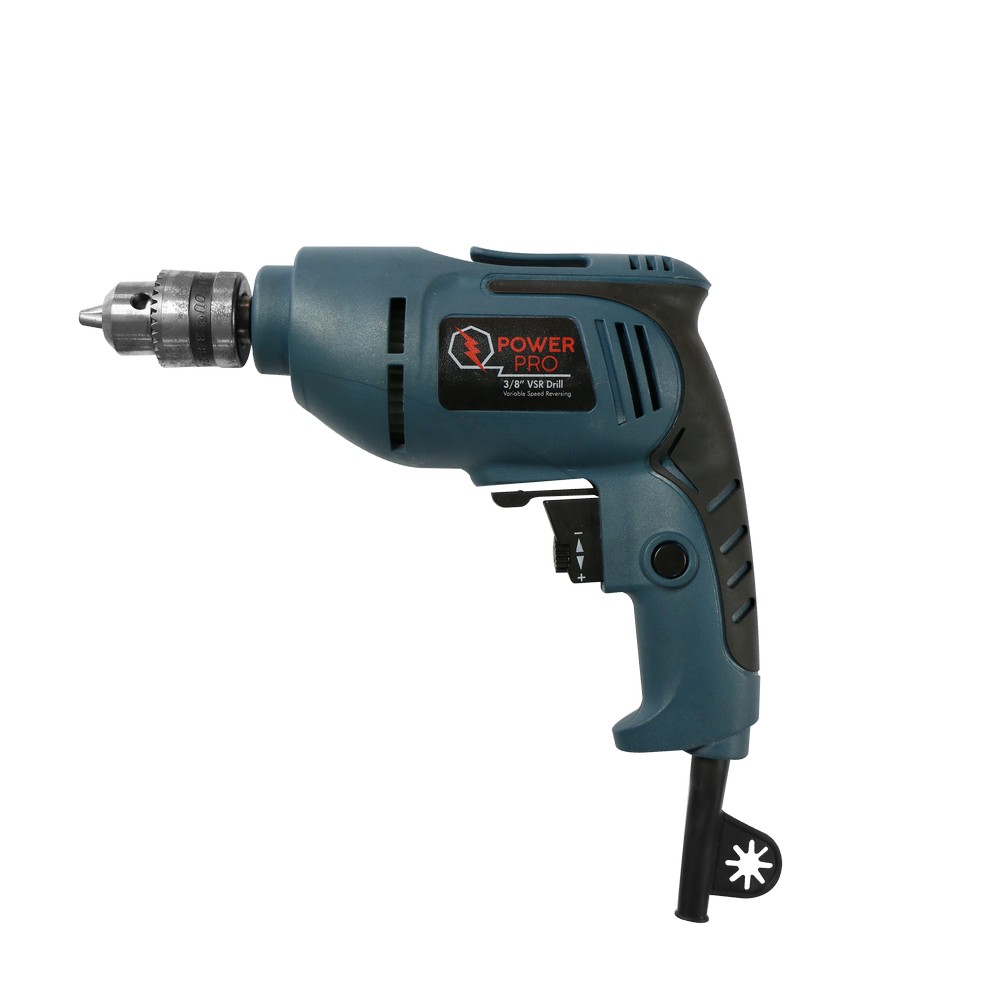
Partes de una
broca:
- Cola: parte que se fija al taladro.
- Cuerpo: Parte activa de la broca. Lleva unas ranuras en forma de hélice.
- Punta: Parte cónica que hace el corte.
Elección de la
broca: Se debe tener en cuenta el tamaño del agujero, la dureza del material y
el afilado de la broca.
- Tamaño: según la magnitud del orificio.
- Dureza del material: Determina el ángulo de la punta de la broca. A mayor dureza, mayor debe ser el ángulo.
- Afilado: La forma de la punta determina el tipo de material para la que se emplea (madera, metal, pared,…). Las brocas para perforar madera terminan en punta o pala. Las de pared cuentan con una pastilla de carburo metálico en la punta (vidia) y las de metal están fabricadas con acero rápido y tienen un ángulo de punta alto.
La cepilladora
dispone de un cilindro al que se le han conectado una serie de cuchillas que,
al girar, arrancan pequeñas virutas. La herramienta permanece fija mientras la
pieza se mueve en línea recta sobre ella. Se puede controlar la velocidad de
corte (o velocidad del motor), la velocidad de avance de la pieza sobre la mesa
de la cepilladora y la profundidad, que regula el espesor a eliminar.
5. Torno: El torno es una herramienta que permite
fabricar piezas de revolución, es decir, cuya sección transversal tiene forma
circular. Se basa en hacer girar la pieza que hay que fabricar sobre su eje de
rotación al mismo tiempo que la herramienta de corte intercambiable(denominada
cuchilla) avanza longitudinalmente con movimiento uniforme. Esta cuchilla
dispone de un filo para arrancar material en forma de viruta.
El torno consta
de:
- Bancada: parte robusta que sirve de soporte al resto.
- Cabezal fijo: Contiene los órganos de sujeción de la pieza. Un motor le imprime giro al cabezal fijo y, por lo tanto, la pieza gira.
- Cabezal móvil: Se encuentra en el extremo opuesto al cabezal fijo y se puede desplazar por medio de unas guías a lo largo del torno.
- Carro portaútiles: Es el que lleva las cuchillas de corte.
Los movimientos
de trabajo del torno son:
- Movimiento de corte: Por rotación de la pieza
- Movimiento de avance: Es el movimiento lineal de la cuchilla debido al desplazamiento longitudinal de la herramienta.
- Movimiento de penetración: movimiento lineal que penetra en la pieza.
- Cilindrado: Consiste en la obtención de un cilindro recto de una longitud y diámetro determinado.
- Refrentado: En este caso, la pieza no presenta el movimiento de avance, sino únicamente el de profundidad de pasada. Su fin es rebajar una pieza
- Ranurado: se trata de abrir ranuras en las piezas: es por lo tanto, un cilindrado obtenido en una franja estrecha.
- Roscado: Es un cilidrado realizado con velocidad de avance altas, mucho mayores que las de giro de la pieza. De este modo, se marca una hélice que definirá una rosca (de un tornillo).

Materiales de las herramientas de corte
- Aceros de alto contenido carbono. Limitan el contenido de carbón de .8 a 1.2%, estos aceros tienen una buena templabilidad y con un tratamiento térmico apropiado, alcanzan una dureza tan grande como cualquiera de las aleaciones de alta velocidad. A máxima dureza, el acero es muy quebradizo, si se desea algo de tenacidad se debe obtener a costa de la dureza.
- Aceros de alta velocidad. Son de alto contenido de aleación, tienen una excelente templabilidad y mantendrán un buen filo cortante a temperaturas de cerca de 650° C. La capacidad de una herramienta para resistir al ablandamiento en altas temperaturas es la dureza al rojo. Estos aceros se crean añadiendo al acero, 18% de tungsteno y 5.5% de cromo.
- Aleaciones fundidas no ferrosas. Se pueden usar al doble de la velocidad de corte y aun mantener el mismo avance. Sin embargo, son más quebradizas, no responden al tratamiento térmico y se pueden maquinar solamente por esmerilado. Se pueden formar herramientas intrincadas por medio de vaciado en moldes de cerámica o de metal y terminando su forma por esmerilado. Sus propiedades se determinan por el grado de acerado que se da al material al vaciarse.
- Carburos. Se hace solo por la técnica de metalurgia de polvos; los polvos de metales de carburo de tungsteno y el cobalto se forman por compresión, se presintetizan para facilitar su manejo y acabado de su forma final, se sinterizan en un horno con atmósfera de hidrógeno a 1550° C y se terminan con una operación de esmerilado.
- Diamantes. Son usados como herramientas de una sola punta para cortes ligeros y altas velocidades deben de estar rígidamente soportados debido a su alta dureza y fragilidad. Se emplean ya sea para materiales difíciles de cortar con otros materiales para herramientas, o para cortes ligeros de alta velocidad en materiales blandos, en los que la precisión y el acabado superficial son importantes. Se usan comúnmente en el maquinado de plásticos, hule duro, cartón comprimido y aluminio con velocidades de corte de 300 a 1500 m/min.
Clasificación de las Máquinas-Herramientas
- Por la forma de trabajar las máquinas herramientas se pueden clasificar en tres tipos:
- De desbaste o desbastadoras, que dan forma a la pieza por arranque de viruta.
- Prensas, que dan forma a las piezas mediante el corte, el prensado o el estirado.
- Especiales, que dan forma a la pieza mediante técnicas diferentes, como por ejemplo, láser, electroerosión, ultrasonido, plasma, etc.
Entre las máquinas convencionales tenemos las siguientes
máquinas básicas:
2. Taladros, destinados a perforación, estas máquinas herramientas son, junto con los tornos, las más antiguas. En ellas el trabajo se realiza por medio del giro de la herramienta y la pieza permanece fija por medio de una prensa. El trabajo realizado normalmente, en los taladros, es hecho por una broca que realiza el agujero correspondiente. También se pueden realizar otras operaciones con diferentes herramientas, como avellanar y escariar.
3. Fresadora, con la finalidad de la obtención de superficies lisas o de una forma concreta, las fresadoras son máquinas complejas en las que es el útil el que gira y la pieza la que permanece fija a una bancada móvil. El útil utilizado es la fresa, que suele ser redonda con diferentes filos cuya forma coincide con la que se quiere dar a la pieza a trabajar. La pieza se coloca sólidamente fijada a un carro que la acerca a la fresa en las tres direcciones, esto es en los ejes X, Y y Z.
4. Pulidora trabaja con un disco abrasivo que va eliminando el material de la pieza a trabajar. Se suele utilizar para los acabados de precisión por la posibilidad del control muy preciso de la abrasión. Normalmente no se ejerce presión mecánica sobre la pieza.
5. Limadora o perfiladora, se usa para la obtención de superficies lisas. La pieza permanece fija y el útil, que suele ser una cuchilla, tiene un movimiento de vaivén que en cada ida come un poco a la pieza a trabajar, que cuenta con mecanismo de trinquete que avanza automáticamente la herramienta (cuchilla).
6. Cepilladora, al contrario de la perfiladora, en la cepilladora es la pieza la que se mueve. Permite realizar superficies lisas y diferentes cortes. Se pueden poner varios útiles a la vez para que trabajen simultáneamente.
7. Sierras, son de varios tipos, de vaivén, circulares o de banda. Es la hoja de corte la que gira o se mueve y la pieza la que acerca a la misma.
No convencionales
1. Arco de plasma, se utiliza un chorro de gas a gran
temperatura y presión para el corte del material.
2. Láser, en este caso es un potente y preciso rayo láser el
que realiza el corte vaporizado el material a eliminar.
3. Ultrasónica, haciendo vibrar un útil a
velocidades ultrasónicas, por encima de los 20.000 Hz y utilizando un
material abrasivo y agua se van realizando el mecanizado de la pieza por la
fricción de las partículas abrasivas. Se usa para trabajar materiales muy duros
como el vidrio, el diamante y
las aleaciones de carburos.
Clasificación de las Virutas
- Viruta continúa: Se suele formar con materiales dúctiles a grandes velocidades de corte y/o con grandes ángulos de ataque (entre 10° y 30°). La deformación del material se efectúa a lo largo de una zona de cizallamiento angosta, llamada primera zona de corte. Las virutas continuas pueden, por la fricción, desarrollar una zona secundaria de corte en la interface entre herramienta y viruta. Dicha zona secundaria se vuelve más gruesa a medida que aumenta la fricción entre la herramienta y la viruta.
- Viruta de borde acumulado: Consiste en capas del material de la pieza maquinada, que se depositan en forma gradual sobre la herramienta. Al agrandarse, esta viruta pierde estabilidad y termina por romperse. Parte del material de la viruta es arrastrado por su lado que ve a la herramienta y el resto se deposita al azar sobre la superficie de la pieza. A medida que aumenta la velocidad de corte, disminuye el tamaño del borde acumulado. La tendencia de formación del borde acumulado se reduce disminuyendo la velocidad de corte, aumentando el ángulo de ataque, utilizando una herramienta aguda con un buen fluido de corte.
- Viruta escalonada o segmentada: Son semi continuas, con zonas de alta o baja deformación por cortante. Los metales de baja conductividad térmica y resistencia que disminuye rápidamente con la temperatura, como el titanio, muestran ese comportamiento. Las virutas tienen un aspecto de diente de sierra por la parte superior.
- Virutas discontinuas: Consisten en segmentos que pueden fijarse, firmemente o flojamente entre sí. Se suelen formar bajo las siguientes condiciones: Materiales frágiles en la pieza, porque no tienen la capacidad de absorber las grandes deformaciones cortantes que se presentan en corte; Materiales de la pieza que contienen inclusiones e impurezas duras, o que tienen estructuras como las láminas de grafito en la fundición en gris; Velocidades de corte muy bajas o muy altas; Grandes profundidades de corte; Ángulos de ataque bajos; Falta de un fluido de corte eficaz; Baja rigidez de la máquina herramienta.
- Viruta en forma de rizos: Se obtiene al trabajar aceros blandos, cobre, plomo, estaño y algunos materiales plásticos con altas velocidades de corte. Todas las virutas desarrollan una curvatura al salir de la superficie de la pieza. Entre los posibles factores que contribuyen al fenómeno están la distribución de esfuerzos en las zonas primaria y secundaria de corte, los efectos térmicos, las características del endurecimiento por trabajo por material de la pieza y la geometría de la cara de ataque de la herramienta de corte. También, las variables del proceso y las propiedades del material afectan al formado de rizos de la viruta. En general, el radio de curvatura baja (la viruta se enrosca más) a medida que disminuye la profundidad de corte; esto aumenta el ángulo de ataque y disminuye la fricción entre herramienta y viruta. Además, el uso de fluidos de corte y de diversos aditivos en el material de la pieza influye en el formado de rizos.
Clasificación de las fuerzas y tensiones de la formación de Virutas
La herramienta de
corte, al penetrar con su filo en el material, provoca la separación de una capa del mismo, que constituye la
viruta.
La determinación determinación de
la fuerza de corte en el mecanizado permite conocer, no sólo las solicitaciones dinámicas a las
que se ve sometidas la herramienta y la pieza, sino
también el valor de la potencia requerida para poder efectuar el proceso. La mayor parte de dicha potencia se consume en la eliminación del material de la pieza; de ahí
que la componente de la fuerza que reviste una mayor importancia desde este punto de vista es aquella que tiene
la misma dirección que la velocidad de corte. A esta
componente componente se la denomina denomina Fuerza de Corte (Fc).
ilustrativo por las imagenes y va al grano, me gusta.
ResponderEliminar